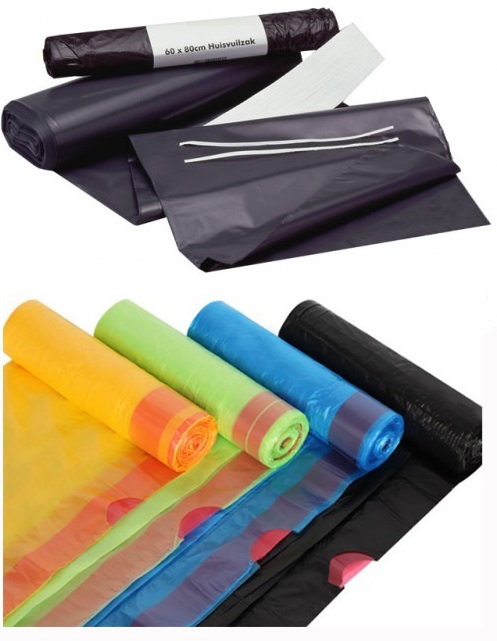
Static electricity on bagmaking machinery: a problem and a help
Bag making machines come in various configurations based on the type of bags produced by the machine. The bag making machine produces a bag by unwinding a roll of plastic film through a series of operations like (heat) sealing, cutting, slitting & stacking. Typical products are garbage bags, T-shirt bags, shopping bags and bags with a draw-tape.
Bagmaking machinery creates a lot of static electricity. Because of the construction of the machinery, the rollers create friction between the roller material and the plastic foil that is passing. This friction creates electrostatic charges on the surface of the material (bags).
These electrostatic charges can cause the machine run poorly, making bad stacks so decreasing production yields and increasing rejects. These kind of problems are recognizable on most types of bagmaking machinery such as Bags-on-Roll (interleaf) and Bag-on-Bag
(for instance with a wicketer). These machines can be found in multiple
industries like general packaging, food, beverage and medical.
Static elimination
To neutralise electrostatic charges on bagmaking machines, Simco-Ion offers a complete program of static eliminating products. Often applied are the AC static eliminators MEB, MaxION or the ½” Super Service bars (made of Teflon so applicable at the sealing unit: heat resistant). Additionally 24V static eliminators are used such as the Performax IQ Easy (speed), VicinION or ThunderION 2.0 IQ. These are both long range discharging bars, so eliminating the electrostatic charges responsible for stacking problems, especially needed on wicketer machinery.

Note: Drawings and pictures do not show the application one to one, but clarify the situation and approach reality
Generating static
Less well known is the fact that static electricity is used to support a variety of processes, especially on bag making machines. It is applied for charging a roll, in example of garbage bags, to prevent air inclusion, further disturbances in the process and keep the roll compact. Also sticking material to a metal roller, without air inclusion, optimizes the cooling process.
Charging of the last bag of a roll, fixes the end of the roll and facilitates the following packing much easier into an outer carton. In many processes static charge is applied to improve production control by charging the bottom and/or side fold of the material or to assist during transport and stacking in the machine.
Perforation detection
The controlled generation of sparks is also used to detect perforations (pinholes), for quality inspection purposes.
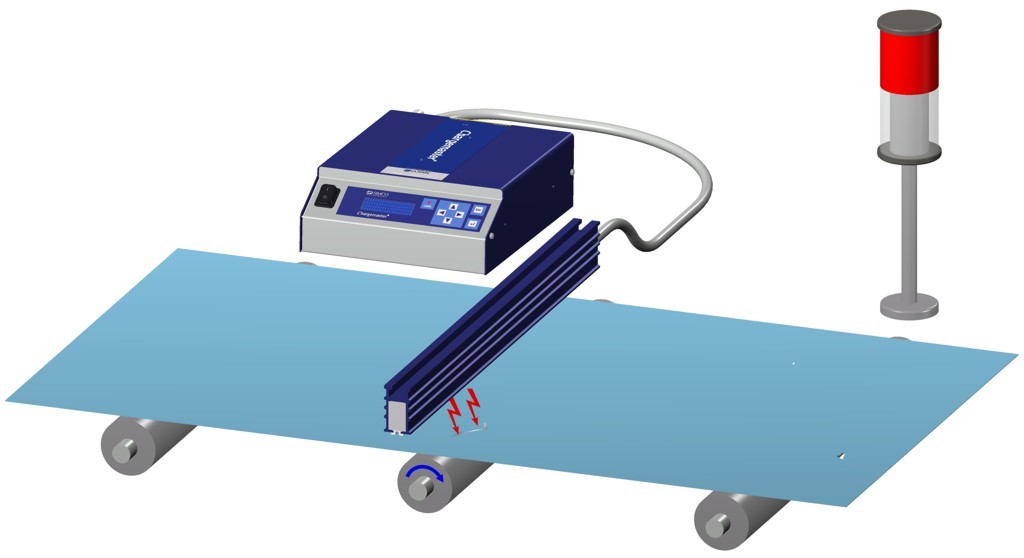
Besides the fact that this is an interesting solution for non-contact inspection of product quality, there is also the possibility to count the number of perforations (also for biodegradable bags).

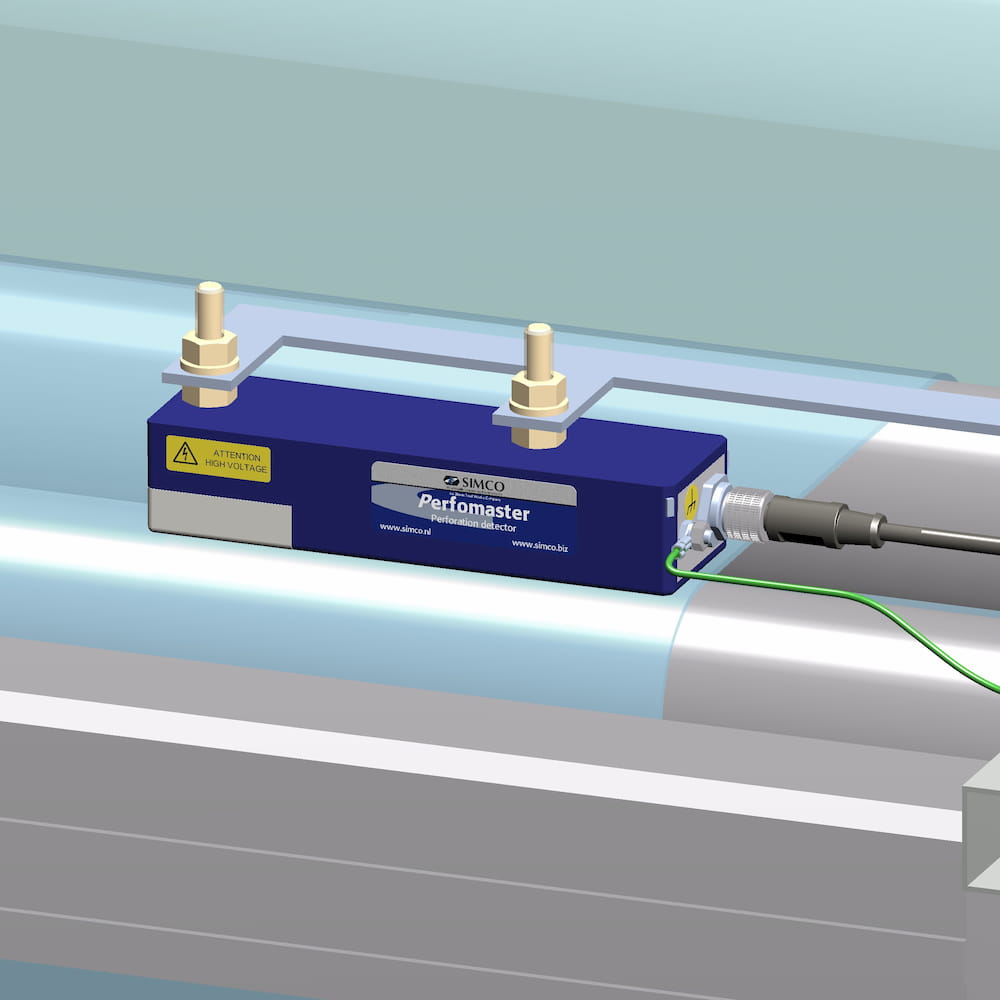
This production technique is made possible by Simco-Ion high voltage generators, that are especially designed for this applications. With a high voltage static generator like the Simco CM5 generator or a Simco 24V Perfomaster the spark can be controlled and converted to a signal that is passed on the machine PLC. This data informs the PLC, so operators knows if a product has a defect, if it is in the right position or the number of products which have been produced.
These Simco-Ion charging and discharging techniques result in high quality, competitive bagmaking!
Are you interested to learn more about the effects of static electricity on your bagmaking machinery? Find a Simco representative near you or subscribe to the Youtube channel Simco-Ion static control Europe